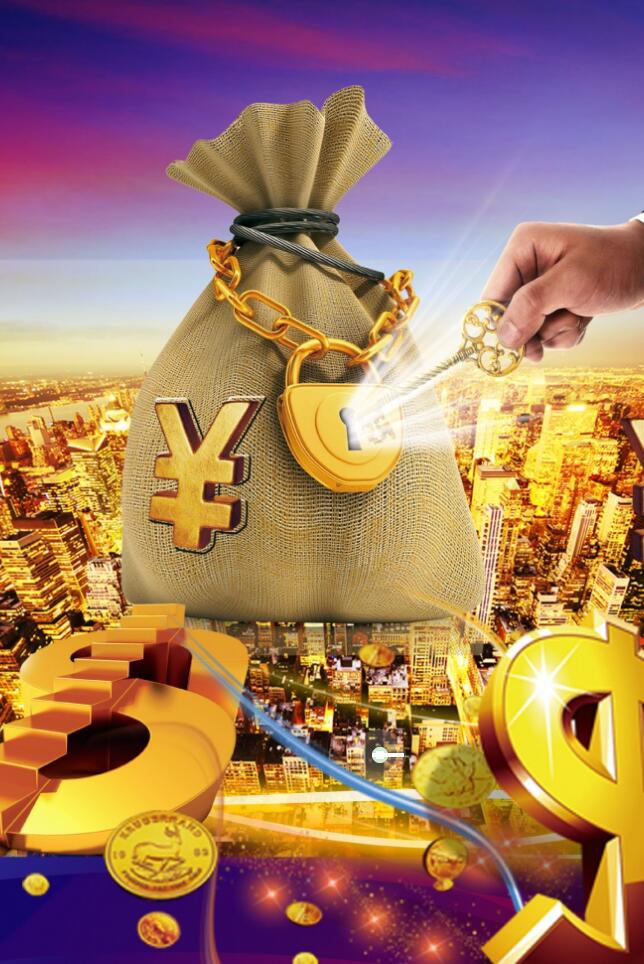
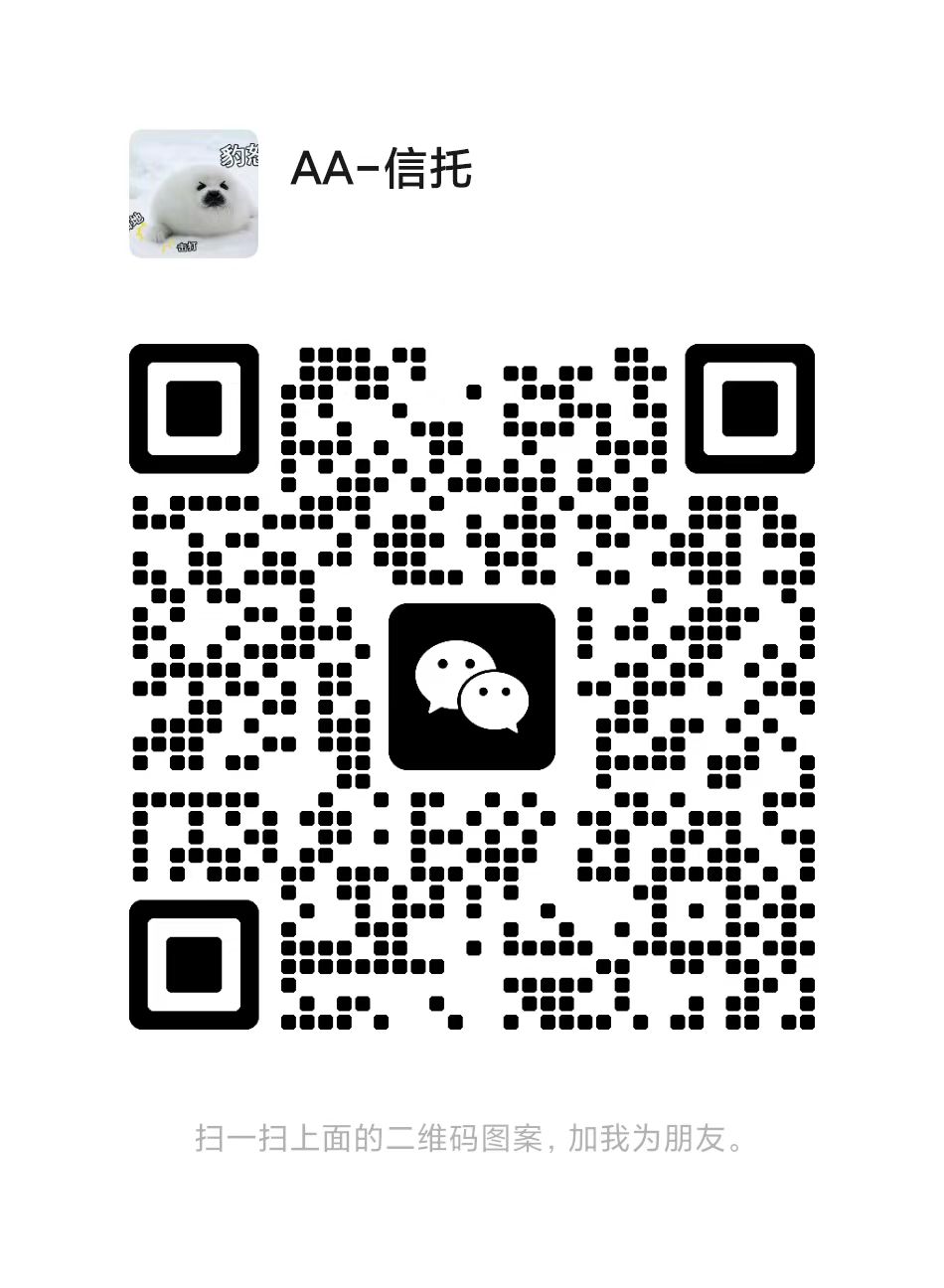
添加微信好友, 获取更多信息
复制微信号
江苏盐城纯地级市政信!
均AA发债主体,盐城市级平台
非网红平台,融资极少!
【中国央企信托-199号盐城地级市政信】
3亿,24个月,自然季度付息
收益:100万:7.52%/年税后
AA市级政府平台担保:盐城城镇化,盐城市人民政府100%控股,AA发债主体,总资产467.8亿,具有较强的担保能力。
AA市级政府平台融资:盐城盐龙湖,实控人为盐城市人民政府,AA发债主体,总资产94亿,履约能力较强。
盐城,江苏省地级市,是江苏省面积最大,海岸线最长的地级市;同时拥有空港及海港两个一类开放口岸的地级市;属于上海一小时经济圈,发展潜力巨大!2022年GDP高达7079亿元,一般公共预算收入453亿元,同口径增长8.1%(GDP增速2022年全省位列第一位);区域财政收入稳定且持长,经济发达政治行政级别高,还款有保障!
信托定融政信知识:
运用结构动力学以及有限元原理,分别建立了车辆和桥梁动力分析模型,由动力学势能不变值原理”与形成矩阵的“对号入座”法则建立空间振动方程,并对车桥耦合空间响应进行了计算分析,结果表明桥梁响应和列车脱轨系数、轮重减载率均满足相关规定,为同类桥梁设计提供参考关键词:钢管混凝土拱桥,车桥耦合,空间振动方程 钢管混凝土拱桥是一种由混凝土和钢材两种材料组合而成的新型桥型,在钢管内填充混凝土,由于钢管的径向约束而限制受压混凝土的膨胀和钢管的套箍作用,使混凝土处于三向受压状态,从而显著提高混凝土的抗压强度
同时钢管兼有纵向主筋和横向套箍的作用,同时可作为施工模板,方便混凝土浇筑,施工过程中,钢管可作为劲性承重骨架,其焊接工作简单,吊装重量轻,从而能简化施工工艺,缩短施工工期
为了增强桥梁结构整体的横向刚度,提高了结构的稳定性,拱肋往往采用提篮的形式,这也使得桥梁整体的线形更加优美,鉴于此,大跨度钢管混凝土提篮拱桥具有很好的发展前景
目前我国已有多座钢管混凝土拱桥处于设计施工阶段,但是针对该类型桥梁的动力特性研究成果甚少
因此,该类桥梁的车-桥耦合动力性能进行研究将有着十分重要的工程意义【1】
1 工程概况 某上承式钢管混凝土拱桥,总体布置图如图1所示
下部拱的跨径为240m,拱肋轴线矢高58m,矢跨比约为1/4.14,拱轴系数3.2,提篮拱倾斜角度7.50
拱肋由四根φ1100mm钢管组成,拱肋外边缘宽度为3.0m,高度为5.7m,其上、下弦各由两肢钢管与其间的钢板连接而呈哑铃形,上行弦钢管和钢板围成的空腔内均灌注#50微膨胀膨胀混凝土,上下之间用工字钢板连接成为桁架形式
从拱趾起两跨21.15m梁范围内,上下弦之间采用实腹板,每块实腹板由两块钢板及内填的C50微膨胀砼构成
拱上桥面结构采用3联4×21.15m钢—砼连续结合梁,桥梁全长为494.68m
钢主梁采用4片工字梁,主梁横向间距3m,每片工字钢梁高2.5m,腹板2420×40mm,上翼缘800×40mm,下翼缘800×40mm,钢主梁采用Q345qD钢,桥面板混凝土强度等级为C50,传剪器采用φ22圆柱头栓钉
混凝土桥面板厚20~35cm,宽2m
图2为结合梁截面图,图3为拱肋典型截面构造图
桥梁的二恒取173KN/m,设计速度为250km/h客运专线,双线行车,线间距为5m
2 有限元模型的建立 2.1 桥梁有限元模型 拱肋、拱肋间联结系,拱上立柱以及主梁工字梁均采用空间梁元模拟,采用板单元模拟混凝土桥面板,钢材及混凝土弹性模量E和泊桑比μ按现行桥规取值
桥梁三维有限元划分如图4所示
2.2 车辆模型 在计算分析车辆(机车)空间振动模型时,本文采用以下假定: (1)假设轮对、转向架和车体在运动过程中均作微振动; (2)假设轮对与钢轨沿铅垂方向密贴,即具有相同的竖向位移; (3)假设车体、转向架和轮对为刚体; (4)假设所有阻尼均为粘滞阻尼,蠕滑力按线性计算,所有弹簧均为线性; (5)忽略机车、车辆纵向振动及其对行车速度以及桥梁振动的影响; (6)忽略构架点头运动及轮对侧滚和点头运动; 这样,每个轮对有2个自由度,包含侧摆和浮沉;每个构架则有4个自由度,包含侧摆、侧滚、摇头和浮沉;车体有5个自由度,包括侧摆、侧滚、摇头、点头、和浮沉
假设客车及机车均按二系弹簧计算,则每辆车(包括机车)共有4×2+2×4+5=21个自由度
2.3 空间振动方程的建立与求解 本文在形成空间振动方程时,首先运用达朗伯原理建立车桥系统运动方程,将列车与桥梁视为为一个耦合的整体体系,然后采用曾庆元院士提出的“动力学势能不变值原理”【2】与形成矩阵的“对号入座”【3】法则建立桥梁刚度、质量、阻尼等矩阵,形成系统的空间振动矩阵方程: 式(1)中, 分别为车桥系统在t时刻的加速度、速度、位移参数列阵
如果直接求解上述方程,只能得到桥梁在列车重力和风荷载作用下的车桥系统的振动响应
考虑到轨道不平顺的作用对车桥系统振动响应有重要影响,所以对方程的左边相应的振动参数如果采用构架人工蛇形波或者实测蛇形波来代替,就可以解出桥梁在列车重力、风荷载以及轨道随机不平顺共同作用下的空间振动响应
3 计算结果 3.1 桥梁自振特性 桥梁的自振频率是由桥梁结构的质量和刚度的分布情况决定的,不同的结构有不同的自振频率,由于在计算时往往采用振型叠加法分析结构的动力响应,,因此分析结构自振特性是分析桥梁动力特性的基础
表1给出了该桥前5阶自振频率值以及相应振型特点,该桥梁第一阶横向振型和第一阶竖向振型如图5和图6所示
计算结果表明该桥第一阶振型为拱梁对称横弯,自振频率为0.6877Hz,第二阶振型为墩梁纵飘、拱梁反对称竖弯,自振频率为0.7008Hz,表明面内刚度大于拱肋面外刚度,但二者自振频率数值相差不大,表明拱肋的宽跨比选择比较合适,具有良好的动力性能
3.2 车桥耦合动力响应 根据前述计算模型与计算原理对列车—桥梁时变系统空间振动响应进行了计算,分别考虑了按单向和双向行车时CRH2型客车、日本500系客车和德国IC3高速客车,以160~300km/h通过桥梁时的车桥动力响应,轨道不平顺采用德国低干扰轨道谱模拟
3.2.1 桥梁空间动力响应 表2为单、双线行车时桥梁振动响应计算结果
为了简便,表中各项响应均只给出最大值
图7为CRH列车通过时跨中和拱顶横向位移与速度的关系图
图8为CRH列车通过时跨中和拱顶竖向位移与速度的关系图
计算结果表明,桥梁横向位移均较小,单线跨中横向最大位移为1.02mm,双线为0.81mm,单线拱顶横向最大位移为0.38mm,双线为0.32mm,说明桥梁横向刚度较大
横向位移随车速的变化不明显,且双线横向位移小于单线横向位移,是由于双线行车时对桥梁横向振动相互削弱所致;竖向位移随车速的提高曾增大趋势,但增大幅度很小,双线行驶比单线行驶的竖向位移大,单线跨中竖向最大位移为5.4mm,双线为6.67mm,单线拱顶竖向最大位移为3.88mm,双线为6.76mm,该桥竖向振幅满足铁路桥梁检定规范的要求,该桥竖向刚度满足要求
3.2.2 列车空间动力响应 表3所示为车辆响应计算结果,图9和图10分别为CRH列车的脱轨系数和轮重减载率与列车速度的关系图
列车运行安全性与舒适性(平稳性)的评定指标选取如下: 脱轨系数:≤0.8 轮重减载率:≤0.6 车体振动加速度:竖向≤ 0.25g;横向≤ 0.20g(中速:≤ 200km/h) 竖向≤ 0.13g;横向≤ 0.10g(高速:≥ 200km/h) 舒适性评价指标:优 良 < 2.50 良 好 2.50~2.75 合 格 2.75~3.00 从图9和图10可以得出,当CRH列车通过该桥时,列车脱轨系数及轮重减载率、轮轨横向摇摆力等都是随着车速的增加而增大,车辆的最大脱轨系数为0.39,最大轮重减载率为0.51,最大竖向加速度0.94m/s2,最大横向加速度0.90m/s2,最大横向Sperling舒适性指标为2.76,竖向Sperling舒适性指标为2.77,亦很好满足前述安全性要求
因此,列车行车通过该桥时的安全性可以得到保证
综上所述,本文所分析提篮式钢管混凝土拱桥设计方案具有足够的横、竖向刚度,列车通过桥梁时满足安全性要求,乘座舒适性达到“合格”标准
4 结论 1,在所有计算工况下,桥梁动力响应均满足要求;各车的车体竖、横向振动加速度满足限值要求
2,在运营速度段及检算速度段所有计算工况下,列车行车安全性满足要求
3,在运营速度段(160~250km/h)所有计算工况下,旅客列车的乘坐舒适度均达到“良好”标准以上;在检算速度段(250~300km/h)所有计算工况下,旅客列车的乘坐舒适度均达到“合格”标准以上
4,该提篮式钢管混凝土拱桥设计方案具有良好的动力特性及列车走行性,可以满足列车安全舒适通过的要求,对同类桥梁的设计也具有一定的参考价值
参考文献 【1】 李波,郭向荣. 铁路大跨度钢管砼提篮拱桥车桥耦合振动分析【J】.西部交通科技,2008,9:78-80 【2】 曾庆元,郭向荣. 列车桥梁时变系统振动分析理论与应用【M】.北京:中国铁道出版社,1999. 【3】 曾庆元,杨平. 形成矩阵的“对号入座”法则与桁段有限元法【J】.铁道学报,1986,8(2):48-59. 【4】 罗浩,郭向荣. 大跨度提篮拱桥车桥耦合振动分析【J】.振动与冲击,2007,27(2),148-149. 【5】 TB/T 2360-1993,铁道机车动力学性能试验鉴定方法及评定标准【S】. 【6】 GB/T 5599-1985,铁道车辆动力学性能评定和试验鉴定规范【S】. 同时对底座板在施工中常见质量问题提出了控制措施,希望为以后底座板施工提供借鉴经验
关键词:底座板 施工 技术 1 CRTSⅡ型无砟轨道系统概述 CRTSⅡ型无砟轨道的施工技术是在引进德国博格板的施工技术基础上,结合我国高速铁路、客运专线发展需要及工程特点,经过消化、吸收、再创新的国产化研究,形成了具有中国特色的无砟轨道施工技术,它具有高精度、高平顺性、高稳定性的显著特点
现已应用于京津城际、京沪高铁、京广客专、沪昆高铁等高速铁路工程,成为了我国目前高速铁路无砟轨道施工的主要施工技术之一
CRTSⅡ型无砟轨道由钢轨、弹性扣件、轨道板、水泥乳化沥青砂浆垫层、底座板(或水硬性混凝土支撑层)等部分组成,系统结构如图1所示
2 桥面底座板概述 底座板是CRTS-Ⅱ型无砟轨道板的支撑基础和结构元件,通过底座板可以作出轨道超高设置
底座板通过由土工布和薄膜构成的滑动层铺设在桥梁上,底座板宽2.95 m,直线段平均厚度为200 mm,曲线地段根据超高设计情况计算确定,长尾通桥连续,是一块配置非预应力钢筋的钢筋混凝土板带
底座板通过梁上剪力齿槽内的剪力构件与梁体剪切连接
3 底座板施工单元划分原则 3.1 施工单元划分 由于桥上CRTS II型板式轨道底座无法一次施工完成,因此必须划分成几个施工单元,根据桥的长度和施工组织方案确定施工段长度,一般为4~5 km,施工单元的首尾位置应设置端刺或临时端刺,临时端刺长约800 m,端刺或临时端刺之间的区段为常规区,常规区一般最短为3个浇筑段,长度约480 m
3.2 临时端刺设置 临时端刺是底座板的一部分,它在桥上暂时起到了路基上常规端刺的作用
左右线临时端刺起点设置应错开两孔简支梁以上,临时端刺区应避开连续梁及其前后各相邻两孔简支梁、道岔区
临时端刺设置的优点是:底座板连接必须在两个端刺之间进行,在长、大桥梁底座板施工过程中,底座板连接有上千个,若要在很短的时间内一次完成所有的连接将给施工带来很大的困难
设置临时端刺后,底座板浇注后的连接就无需在两个端刺之间进行(可在临时端刺和端刺,临时端刺和端刺之间进行),即两临时端刺或临时端刺和端刺之间的底座板就可以作为一个独立的施工单元进行连接施工,这也意味着可以将整个长桥底座板分成若干独立的施工单元,无需等到全桥底座板施工完成后,再开始铺设轨道板,为后续轨道板铺设赢得宝贵时间
3.3 后浇带设置 (1)常规区混凝土浇筑段长度不大于164 m,即5孔简支梁长度
为了避免混凝土浇筑时强制力传入桥墩,在两处混凝土浇筑段之间预留50 cm,设置钢板连接器后浇带(BL1后浇带),其在底座板混凝土浇筑段浇筑时留出,BL1后浇带距离梁端长度不小于5 m
(2)当分段长度大于两跨梁时,底座板与梁端齿槽只进行钢筋连接,浇筑时预留66 cm宽后浇带,称之为剪力齿槽后浇带(BL2);当分段长度为一跨时,底座板在梁端齿槽处一次浇筑
位于浇筑段中心的一个剪力齿槽后浇带(BL2)与底座混凝土同时浇筑,其余简支梁的剪力齿槽后浇带纵连前需要预留不浇筑
此外,该后浇带左右浇筑段长度差不大于15 m
(3)剪力齿槽超过两排时(如连续梁及其两端各两孔简支梁上),齿槽后浇带应与底座混凝土一次浇筑,并设立BL1后浇带
为保证连续梁及相邻两孔简支梁上BL1尽量关于先浇筑的BL2对称,可通过设置自由混凝土浇筑段来满足要求,自由混凝土浇筑段长度不大于80 m
(4)距路基常规端刺最近的BL1后浇带与常规端刺的距离不超过80 m
只有当摩擦板长度在70~100 m之间时,钢板后浇带到常规端刺的距离可以适当加大,保证后浇带位于桥上
另外,常规端刺到先浇筑的剪力齿槽之间的距离不得大于160 m
(5)对于大跨度细杆拱而言,其处理方式同连续梁
即细杆拱及相邻的两孔简支梁上,剪力齿槽要与底座混凝土一起浇筑,并设立BL1后浇带
通过在细杆拱上设置一定数量的自由混凝土浇筑段以满足BL1后浇带关于先浇筑的BL2后浇带的对称要求
(6)钢筋连接器后浇带与轨道板板缝的距离不小于0.7 m
4 底座板施工方法和施工工艺 底座板施工是在桥梁面经过验收,防水层施作完成,并经检测合格后,底座板施工前应对梁面的杂物、灰尘进行清理,才能进行底座施工
4.1 施工工艺流程(见图3) 4.2 安装剪力钉 剪力钉采用HRB335级钢筋与锚固钢板(Q235级钢板),所有剪力钉要测量齿槽的实际深度后加工,剪力钉钢板位置高于1/2底座板厚度,保证剪力钉钢板顶面同底座板上层钢筋保持1~2 cm距离
剪力钉安装前要严格检查,清理剪力齿槽内的杂物和套筒内污物,确保剪力钉拧入深度(不小于42 mm)和拧紧力矩(MA≥140 Nm)
锚固板焊缝应符合《钢筋焊接及验收规程》(JCJ18-2003)等相关规范的规定
4.3 铺设挤塑板 在梁端各1.45 m范围内铺设一层5 cm厚的挤塑板
铺设前,用洁净的高压水及高压风冲洗桥面,确保铺设范围内洁净且无磨损性砂石颗粒
在梁端1.45 m范围满涂刷聚氨酯胶水,在挤塑板上面采用重物满压1 h,使之挤塑板与胶水牢固粘结,保证挤塑板与梁面密贴,避免出现空鼓现象
高强度挤塑板顶面与梁面加高平台顶面间的允许误差为±2 mm,同时挤塑板要与加高平台侧边要紧贴,不得留有空隙
4.4 铺设两布一膜 两布铺设范围内要清扫洁净且无磨损性砂石颗粒,根据滑动层铺设位置,在底座板范围内沿线路纵向两侧及中间各弹出宽30 cm的粘合剂涂刷带,控制聚氨酯的涂刷范围
聚氨酯涂刷好后,马上进行第一层土工布(厚3 mm)的铺设,其铺设范围为桥梁固定端的剪力齿槽内边缘至桥梁活动端梁缝处断开,铺设应从活动支座梁端开始;第一层土工布铺设完成后,直接在第一层土工布上铺设聚乙烯薄膜,其铺设范围为桥梁固定端的剪力齿槽内边缘至相邻桥梁的剪力齿槽外边缘;聚乙烯薄膜铺设好后,即可开始铺设第二层土工布(厚2 mm),其铺设范围为桥梁固定端的剪力齿槽内边缘至相邻桥梁的剪力齿槽外边缘,铺设时可用水润湿土工布以利于将土工布吸附在聚乙烯薄膜上
在铺好的滑动层上按间距50 cm的要求梅花形摆放条形垫块(40×5×4 cm)
一是防止安装钢筋笼时将滑动层刺穿;二是防止大风将滑动层刮起
两布一膜施工注意事项:(1)铺设应平整、无皱褶且无破损,如发现破损,应进行更换,重新铺设
(2)底层土工布可对接,中间薄膜可采取熔接方式,上层土工布不允许对接
(3)土工布订制幅宽宽度为3.05 m,底座砼施工完成后切除多余部分
(4)两布一膜铺设完成后,在梁端伸缩缝处,两布一膜的上方铺设一块2.95 m×0.3 m×0.003 m的钢板,防止混凝土塌陷到伸缩缝中
4.5 钢筋安装 底座板钢筋采用桥下集中预制和桥上绑扎相结合的方式,在施工便道允许的情况下,在桥下进行集中预制,用专用吊具进行吊装,要确保运输、吊装过程中钢筋网片不变形,吊装时要注意钢筋网片的方向
无论桥下预制钢筋笼还是桥上绑扎,为了确保钢筋定位准确,都应制作钢筋定位模具,同时钢筋加工前要对桥面标高进行实测,根据实测结果,对钢筋加工尺寸进行调整,确保底座板钢筋保护层厚度满足要求
钢筋安装前在两布一膜上放置混凝土垫块(50×5×4 cm,标号与底座板砼同标号C30砼,可适当配一根直径6 mm的钢筋或者更细的钢丝,保证其在运输和施工过程中不折断),防止底座板钢筋铺设使滑动层过度受压而破损
垫块梅花状布置,纵向间隔约80 cm,保证每延米垫块数量不少于8块,垫块与滑动层的接触面积控制在0.185 m2/延米
垫块高度应满足钢筋保护层厚度要求,长度0.35~1 m
纵向钢筋搭接接头采用接头面积百分率不应超过50%,相邻两个搭接区段中心间距应大于1.3倍的钢筋搭接长度
纵向钢筋搭接区段应避开梁缝和剪力齿槽后浇带的钢筋加强区域;纵向钢筋搭接区采用外箍筋,箍筋间距为100 mm;内箍筋与外箍筋交替使用处的纵向钢筋不允许弯折,应通过调整2~3根箍筋的高度进行过渡处理,保证纵向钢筋平顺缓和过渡,同时满足钢筋保护层厚度要求
4.6 模板安装 底座板模板按照一般地段和超高地段两种型式设计,采用可调组合钢模,模板通过调节螺栓进行调平,模板内侧采用可调螺杆内支撑,模板外侧采用可调螺杆对撑,模板加固间距要根据模板刚度来设置,确保模板稳固、混凝土浇筑时模板不变形;模板安设要平顺,相邻模板错台不超过1 mm,确保接缝严密
浇筑前,模板与梁面间的缝隙采用“L”型钢板进行封堵,采用垫块把封堵钢板顶紧,确保与模板紧贴,防止底座板“烂根”现象的发生
4.7 混凝土施工 混凝土浇筑前,除要仔细检查浇筑前的准备工作是否充分外,还要特别注意模型底口封堵是否完好,所有后浇带螺母是否为松开状态(不少于3 cm)
剪力齿槽处方木内撑加固是否稳固,保证剪力齿槽间距均匀,符合规范要求,底座板采用低弹模的C30钢筋混凝土,浇筑时要控制好混凝土坍落度(一般160 mm左右),超高地段地段的坍落度要适当调小一点,否则振捣时水泥浆从低侧流出,而且不利于混凝土顶面找平
底座板关键工序是顶面收光拉毛,顶面收光时应注意标高控制,底座板混凝土顶面标高在误差允许范围内“宁低勿高”,底座板完成后及时组织人员进行复测,否则后期轨道板初铺以后底座打磨难度较大
底座板施工中底座板顶面标高、平整度的控制极其关键,直接影响到后续工期,因此必须高度重视
底座板标高的控制中,往往出现底座板超高,导致砂浆层厚不足的现象,一是底座板可能出现正误差;二是轨道板一般按照正误差控制,一般比设计厚度后3~5 mm,这样造成正误差的累积,就可能导致砂浆层厚不足的现象,控制方法有:一是要尽可能按照设计的底座板顶面标高控制,甚至比设计低2~3 mm,消除轨道板的正误差,能够保证砂浆层的厚度;二是要控制好底座板的平整度,防止出现局部砂浆厚度不足的状况
底座板混凝土采用长柄塑料毛刷横向拉毛,拉毛的好坏对水泥乳化沥青砂浆的灌注质量有很大影响,拉毛深度一般控制在1~2 mm,拉毛太重,不利于砂浆的流动,且在灌注过程中,导致水泥乳化沥青砂浆产生贯穿孔
混凝土浇筑完成后及时覆盖和洒水养护,洒水次数应能保持混凝土处于润湿状态,养护期不低于7 d,模板在混凝土强度达到2.5 MPa以上,其表面及棱角不因拆模而受损时方可拆模
4.8 底座板连接及后浇注带施工 桥梁底座板后浇带分常规区和临时端刺区后浇带,常规区后浇带在底座混凝土浇注完成后,混凝土强度大于15 N/mm2时一次连接并浇注完成;临时端刺区后浇带按要求连接好后,分两次浇注完成:后浇带的连接和浇注符合下述要求:(1)底座板后浇带应在钢筋绑扎好之前完成安装
(2)常规区和临时端刺区后浇带的连接和浇注按先常规区后临时端刺区的施工顺序
(3)连接旃工宜在底座板温度处于20 ℃~30 ℃之间进行,高于30 ℃时严禁进行连接作业,且必须在规定时间内连接完成
(4)后浇带螺母连接拧紧时,必须按要求进行,严禁将用手和扳手拧紧方式混淆
底座板连接时砼强度需达到20 MN/mz,连接操作是围绕并确保板内20℃时零应力状态而进行的后浇带连接筋张拉施工
底座连接施工主要分四种情况:一是新设临时端刺区+常规区+新设临时端刺区;二是固定端刺区+常规区+新建临时端刺区;三是既有临时端刺区+常规区+新设临时端刺区;四是既有临时端刺区+常规区+既有临时端刺区
单元段内的底座板连接施工在单元段内的端刺(两端或临时端刺或固定端刺)及常规区底座板全部施工完成的基础上进行
所有类型单元段底座板的连接施工均应在温差较小的24 h内完成
4.8.1 新设临时端刺区+常规区+新设临时端刺区 两临时端刺区中的基段LP1按接壤常规区方式布设,常规区两端及两临时端刺区后浇带按单元段中心对称原则顺序安排其连接施工,工艺、工序要求如以下几点
(1)临时端刺区的基段LP2、LP3、LP4、LP5的基准测量,于底座板连接前进行,其结果将作为本单元段临时端刺区与下一个常规区连接时进行张拉计算的基础,测量时间尽可能与底座板连接时间靠近,以使连接温度尽可能与测量时的温度接近
①基段LP2、LP3、LP4、LP5的长度测量
基段LP2的长度测量:后浇带BLl-J2面向J2后浇带BLl-J1方向的前方,两者间的距离
; ; 基段LP3、LP4、LP5之间的长度测量:按分段长度进行测量
②基段LP2、LP3、LP4、LP5的温度测量,使用预埋的测温电偶测量,相邻板温不一致时,按两板长度及温度加权平均计算,各段长度与对应温度测量于底座板连接前进行一次,测量结果应准确记录并保存
(2)常规区板温测量,与临时端刺区板温测量一同进行,并据此计算连接筋张拉值
(3)底座板钢筋连接工序
底座板钢筋连接应在板温30 ℃以下的条件下进行,张拉连接时按规定顺序操作,先部分连接,再全部连接完成
1)临时端刺区中的4个后浇带BL1的预连接,按后浇带BLl-J4、后浇带BLl-J3、后浇带BLl-J2、后浇带BLl-Jl的顺序将钢筋连接器螺母用手拧紧
2)首批连接施工,先连接常规区与临时端刺区接壤处KO的前10个常规区后浇带钢筋,后依次连接常规区与临时端刺区接壤处KO、后浇带BLl-Jl、后浇带BLl-J2、后浇带BLl-J3的钢筋,后浇带BLl-J4的钢筋于相邻单元段底座板连接时张拉,同时后浇带BLl-J2、后浇带BLl-J3的钢筋需进行张拉调整
连接分三种情况进行
①当测量板温T<20 ℃时,通过计算确定连接钢筋的张拉距离,其中,后浇带BLl-J3范围内钢筋张拉距离按后浇带BLl-J2的1/3计,其余直接按计算结果采用,此时的拧紧操作应是先用手拧紧,在此基础上,钢筋连接器中的非拧紧端螺母按计算结果松开张拉距离,再用扳手拧紧
②20 ℃≤T≤30 ℃时,钢筋连接器螺母用手拧紧螺母即可,即张拉距离为0
③T>30 ℃时,不允许拧紧螺母,且底座板应采取降温措施,板温在30 ℃以下时再连接
3)补充连接施工,连接常规区其余后浇带连接钢筋,此工序在连接常规区与临时端刺区接壤处KО、后浇带BLl-J1、后浇带BLl-J2、后浇带BL1-J3之后接续进行,连接方法同前述第2)中所述
(4)后浇带BL1混凝土浇注
后浇带钢筋连接完成后应随即进行后浇带混凝士浇注,浇注范围应包括常规区所有后浇带及两临时端刺区中的常规区与临时端刺区接壤处KО、后浇带BL1-J1,浇注工作24 h以内完成,此工序与后浇带连接应接续施工,不留间隔时间,后浇带BLl-J2、后浇带BLl-J3、后浇带BLI-J4于相邻单元段底座板连接后施工
(5)后浇带BL2硷施工,后浇带BL2设于临时端刺区的固定连接处,分为早期固定连接和后期固定连接,早期固定连接在单元段底座板钢筋连接完成3~5 d后进行,位置在基段LP2范围内与基段LP2相邻的两个固定连接后浇带,两临时端刺区后浇带对称施工,后期后浇带BL2砼在相邻单元段底座板连接后施工
4.8.2 固定端刺区+常规区+临时端刺区 此种情况下,连接工序、工艺与“新设临时端刺+常规区+新设临时端刺”相同,区别是不存在两端刺范围对称连接施工问题
4.8.3 既有临时端刺区+常规区+新设临时端刺区 其中的常规区与新设临时端刺的连接与“新设临时端刺+常规区+新设临时端刺”中的方法一致,既有临时端刺区、新设临时端刺区与常规区的连接施工要对应施工,同步完成
(1)既有临时端刺与常规区的连接施工
1)既有临时端刺区后浇带BLl-J4、后浇带BLl-J3、后浇带BLl-J2张拉值的确定,在既有临时端刺区的基段LP2、LP3、LP4、LP5首次基准测量的基础上进行,该基准测量的方法如“新设临时端刺+常规区+新设临时端刺”中所述,需要再次测量既有临时端刺区的基段LP2、LP3、LP4、LP5的长度及板体温度,且应于底座板连接前进行,根据基段LP2、LP3、LP4、LP5第二次温度及长度的测量结果,对比该临时端刺区的首次基准测量数据,计算基段LP2、LP3、LP4、LP5温度荷载下的变形值,以此确定后浇带BLl-J4连接钢筋张拉值并修正后浇带BLl-J3、后浇带BLl-J2钢筋张拉值
2)常规区底座板温度测量,与临时端刺区温度测量同时进行,并据此计算连接筋张拉值,测量方法与“新设临时端刺+常规区+新设临时端刺”同
3)底座板连接钢筋的张拉工序,连接筋张拉施工方法同“新设临时端刺+常规区+新设临时端刺”相关要求
①连接筋张拉预连接施工,连接范围为既有f临时端刺与常规区的接壤处Kl及所有常规区后浇带BL1,连接方式为用手拧紧钢筋连接器螺母;另一端常规区与新设临咐端刺的连接对应施工
②首批连接施工
连接范围为邻靠既有临时端刺与常规区的接壤处K1的至少10个常规区后浇带BL1,张拉连接方式及张拉距离根据底座板温度确定,即按T<20 ℃、20 ℃≤T≤30 ℃、T>30 ℃计3种情况区分,各类情况下的连接工艺同“新设临时端刺+常规区+新设临时端刺”相关要求
③补充连接施工,连接范围为既有临时端刺与常规区的接壤处Kl及常规区所有剩余后浇带BL1,具体工序要求同第②条;另一端常规区与新设临时端刺的连接对应施工
④既有临时端刺区后浇带BLl-J4、后浇带BLl-J3、后浇带BL1-J2的调整张拉,按计算确定的调整张拉值以后浇带BLl-J4→后浇带BL1-J3→后浇带BLl-J2的顺序进行张拉连接,张拉施工应在连接器螺母原有紧固基础上单端调整螺母并张拉,不可解开重张
(2)常规区与新设临时端刺区的连接施工,常规区与新设临时端刺的连接工序、工艺与“新设临时端刺+常规区+新设临时端刺”中的相关要求一致,常规区和新设临时端刺区的连接应与常规区和既有临时端刺的连接对应旅工,相互对应配合工序如下
①既有临时端刺区与常规区进行“连接筋张拉预连接施工”时;另一端常规区与新设临时端刺区的连接则应顺序完成后浇带BLl-J4、后浇带BLl-J3、后浇带BLl-J2、后浇带BLI-J1的钢筋预连接,其连接器螺母用手拧紧
②既有临时端刺区与常规区进行“首批连接施工”时;另一端常规区与新设临时端刺的连接则应完成邻靠常规区与临时端刺区接壤处KО的前l0个常规区后浇带钢筋,张披连接方法同“新设临时端刺区+常规区+新设临时端刺区”相关部分
③既有临时端刺区与常规区进行“补充连接施工”时;另一端常规区与新设临时端刺区的连接则应顺序完成常规区与临时端刺区接壤处KO、后浇带BLl-Jl、后浇带BL1-J2、后浇带BLl-J3的钢筋连接,其后配合既有临时端刺区与常规区的连接施工,一同完成剩余常规区后浇带的钢筋连接,张拉连接方法同“新设临时端刺区+常规区+新设临时端刺区”相关部分
(3)后浇带BLl-JI砼施工,“既有临时端刺区+常规区+新设临时端刺区”模式底座板按上述工序要求完成钢筋连接施工后,立即对既有临时端刺区中的后浇带BLI -J2、后浇带BLl-J3、后浇带BLl-J4及常规区所有后浇带BLl-J1和既有临时端刺区与常规区的接壤处Kl迸行硷灌注施rT,连接与硷灌注工序不出问隔时间,所有砼灌注施工24 h间内完成,新设临时端刺区中的后浇带BLl-J2、后浇带BLl-J3、后浇带BLl-J4待与后续施工单元段连接施工后再灌注砼
(4)后浇带BLl-J2砼旋工,新设临时端刺区巾部的两个固定连接后浇带BL2施工同“新设临时端刺区+常规区+新设临时端刺区”有关要求:既有临时端刺区中的剩余固定连接后浇带BL2砼应于单元段钢筋连接完成10天后进行
4.8.4 既有临时端刺区+常规区+既有临时端刺区 (1)既有临时端刺区后浇带BLl-J4、后浇带BL1-J3、后浇带BL1-J2张拉值的确定,同前述“既有临时端刺与常规区的连接施工”有关要求
(2)常规区底座板温度测量,同前述“新设临时端刺区+常规区+新设临时端刺区抑有关要求
(3)底座板铡筋张拉连接施工,底座板连接施工同“既有临时端刺区与常规区的连接施工”有关要求,两端开展的“既有临时端刺区与常规区的连接施工”应相对于单元段中心对称同步进行
(4)后浇带BL1砼施工,“既有临时端刺区+常规区+既有临时端刺区”模式底座板按上述工序要求完成钢筋连接施工后,立即对两个既有临时端刺区中的后浇带BLI-J2、后浇带BLI-J3、后浇带BLI-J4及常规区所有后浇带BL1和既有临时端刺与常规区的接壤处Kl进行砼灌注施工,施工从两端向单元段中心部位相向对称进行,钢筋连接与砼灌注工序不出间隔时间,所有砼灌注施工24 h间内完成
(5)后浇带BL2砼施工,既有临时端刺区中的剩余固定连接后浇带BL2砼于单元段钢筋连接完成10 d后进行,两既有临时端刺区后浇带BL2砼对称灌注,当天完成
5 结语 板式无砟轨道底座板施工中要应用到很多新工艺,存在一些技术难点:一是临时端刺区底座板的施工工艺复杂,且工序较多,工序之间有着严格的先后施工顺序,临时端刺的平面布置、各后浇带的连接先后顺序和质量都涉及到结构安全;二是施工精度要求高,底座板顶面高程允许偏差为±5 mm,平整度要求为7 mm/4 m;三是大超高段底座板成型困难,混凝土采取泵送施工,混凝土的坍落度大、自流性能好,而大超高地段底座板成型困难,这就需要找到一种既能满足泵送旋工工艺和底座板成型的混凝土配合比;四是技术管理跨度大,底座板施工过程中,有很多工序及工艺涉及到结构安全和工程的使用功能,必须严格控制好,其中任何一个环节出现失误都将给工程质量带来不可预料的后果
本文目的是解决无砟轨道底座板施工中的上述技术难点,提供一种较为可靠的桥梁上无砟轨道底座板的施工方法,以满足无砟轨道底座板的质量、精度要求
参考文献 【1】 TZ216-2007.客运专线无砟轨道铁路
中国央企信托-199号盐城地级市政信